合金冷加工模具钢全面分析讲解
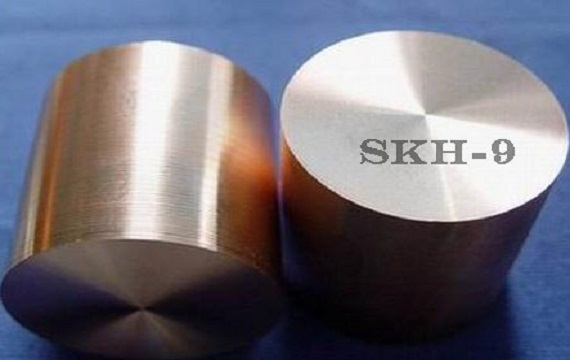
一、合金冷加工模具钢的一般特性合金冷加工模具钢的主要性能有:耐磨性好,工作时刃口锋利;淬火状态具有较高的硬度和一定的淬火深度;淬火安全性好,热处理变形小,复杂断面不易开裂;强度和韧性适当高,工作时叶片不易塌陷或塌陷;良好的加工工艺和成型性。
合金冷作模具钢属于高碳合金钢,碳含量一般在0.8%以上。此外,它还含有铬、钨、钼、锰和钒等合金元素。根据合金元素的含量范围,可分为以下钢类:
高碳低合金冷加工模具钢;高碳高铬冷作模具钢;模具钢空气淬火;基体钢和低碳高速钢;高韧性、高耐磨性的冷加工模具钢;火焰淬火模具钢;将温度保持在600-650℃一定时间,可以减少模具的变形或开裂。通常采用油冷,而形状复杂的模具钢可以分段淬火,等温淬火,以减少淬火变形。在高硬度条件下使用的冷加工模具钢通常在低温(150-200℃)下回火,以消除一些淬火内应力,提高高模具钢的强度和韧性,同时保持高硬度。回火温度(300-350℃)只有在高弹性、大动载荷下使用时才升高,此时硬度降低。
2.高碳高铬冷作模具钢:高碳高铬冷作模具钢包括:Cr12、Cr12MoV、D2(Cr12Mo1V1);它具有硬度高、强度高、耐磨性高、淬火变形小的优点;属于莱氏体钢,改善模具钢中碳化物分布是提高模具钢质量的重要途径。
热处理特点分析:高碳高铬冷作模具钢的主要性能(硬度、强度、塑性、韧性、红硬性、调质的体积变形)与淬火温度有很大关系,即淬火温度决定了所生产模具的使用条件;例如:
1.低温淬火和低温回火可以获得较高的力学性能和较小的变形。适用于高负荷或复杂形状的模具和冷轧模具。
2.高温淬火和高温回火可以获得较高的红硬性和耐磨性,但力学性能低,变形量大。适用于制造承受载荷小但要求耐磨性高的模具,工作温度在400-500℃。
3.对于一些要求高韧性的冲压模具或挤压模具,可采用贝氏体等温淬火处理。此时的显微组织为下贝氏体+马氏体+粒状碳化物+少量残余奥氏体。获得部分贝氏体组织后,硬度略有下降,但韧性明显提高,模具变形减小。
另一种减少模具变形的工艺方法是真空淬火。在工业生产中,高碳高铬冷作模具钢经常回火2-3次,以提高前回火残余奥氏体对初生马氏体的韧性,或减少残余奥氏体第二阶段转变形成的粗大碳化物对韧性的影响。简而言之,多次回火用于提高模具钢的韧性。
Iii.高速钢W6Mo5Cr4V2、SKH-9、M2和W18Cr4V的淬火和回火要求。在工业应用中,淬火温度应根据模具的工作条件和应用要求来选择
1.具有高电阻(一般约2500兆帕)和适当韧性的模具,如挤压模具;可以选择较高的淬火温度;
2.形状复杂或压力低、韧性差的模具应采用较低的淬火温度。至于淬火冷却,可以根据模具的工作要求选择油淬、风冷或分段淬火。在工业应用中,回火一般使用三次,每次回火应冷却至室温,以保证残余奥氏体转变为马氏体。每次回火都能提高残余奥氏体向初生马氏体转变的韧性,从而提高高速钢的韧性。
4.高韧性高耐磨冷作模具钢近年来,我国开发了一系列含铬、钼、钒约8%的高韧性高耐磨冷作模具钢;例如,DC53模具钢的总合金含量约为12%。由于碳化钒在模具钢中均匀细小地形成和分布,所以模具钢具有高耐磨性和良好的韧性。这种模具钢淬透性高。
V.火焰淬火模具钢由于工业产品的快速升级,要求缩短模具的生产周期,简化热处理工艺。20世纪70年代,国内外开发了一系列适用于火焰淬火工艺的特种冷作模具钢。例如SX5(Cr8MoV)、SX105(7CrMnSiMoV)、HMD-1(Cr4MnSiMoV)、7CrMnSiMoV;
火焰淬火模具钢的特点如下:
1.允许淬火温度范围宽,即使在100-250℃淬火也能达到满意的效果;
2.空冷淬火可获得良好的淬透性、较高的表面硬度和芯部硬度;
3.淬火后,工件变形小;
4.强度、韧性、耐磨性好;
5.焊接性好,可采用堆焊修复技术;
6.加工性能好。